Cathodic Protection: Why You Need It!
Picture this: You’ve invested heavily in your well pipelines, only to watch them slowly succumb to the silent but deadly threat of corrosion. It’s a frustrating and expensive problem, leaving you questioning how you can protect your valuable assets. But what if there was a solution that could put an end to your worries and safeguard your pipelines for years to come?
Enter cathodic protection, a tried and true method of corrosion protection that has saved countless buried or submerged structures from decay. Imagine the relief of knowing that your pipelines are shielded by an invisible armor, a sacrificial anode taking the brunt of the damage so your precious infrastructure remains unscathed. With a well-designed cathodic protection system, your pipelines can enjoy a longer, healthier life, free from corrosion.
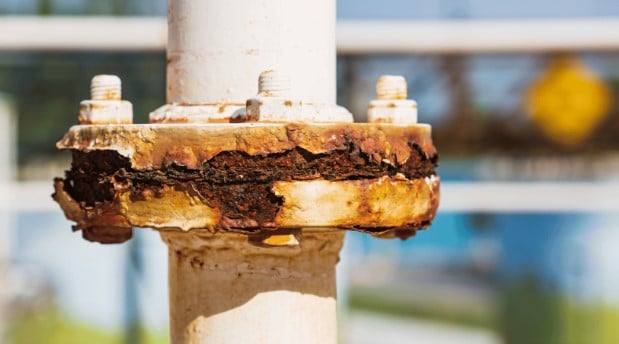
What is Cathodic Protection?
Cathodic protection is a highly effective corrosion protection technique that safeguards metallic structures, such as pipelines, storage tanks, and reinforced concrete structures, from the damaging effects of electrochemical corrosion.
When metallic structures are buried or submerged, they are exposed to moisture, soil, or other electrolytes, which can cause corrosion over time. The corrosion process is essentially an electrochemical reaction that results in the deterioration of the metal, compromising its structural integrity and potentially leading to costly repairs or replacements.
What are the Two Types of Cathodic Protection Systems?
There are two primary types of cathodic protection systems: sacrificial (or galvanic) and impressed current cathodic protection (ICCP). Both systems use similar principles but differ in the way cathodic protection current flows and the components they use.
Sacrificial Cathodic Protection
In sacrificial cathodic protection, galvanic anodes made from a more active metal than the protected structure, such as zinc galvanic anodes, are connected to the metallic structure. This creates a galvanic system where the anode material, or the sacrificial metal, corrodes in place of the protected metal.
The anode surface acts as the source of the cathodic protection current that flows to the protected structure, preventing the electrochemical corrosion process from occurring on the metal surface.
This type of protection is considered passive, as it doesn’t require an external power supply. The sacrificial anodes are designed to have a limited anode life and must be replaced periodically to ensure continuous protection.
Soil resistivity and the type of anode, such as high silicon cast iron or mixed metal oxide, can influence the performance and lifespan of the sacrificial cathodic protection system.
Impressed Current Cathodic Protection (ICCP)
Impressed current cathodic protection systems utilize an external DC power source, like a cathodic protection rectifier, to drive the cathodic protection current flow. The impressed current anodes used in ICCP systems are made of metal oxide or silicon cast iron, which are resistant to accelerated corrosion and have a longer anode life.
In ICCP systems, the anode materials are connected to the positive terminal of the outer power supply, while the metallic systems are connected to the negative terminal. This creates a direct current voltage gradient that forces the current flows to the protected structure, providing corrosion protection.
ICCP systems can be more effective in controlling corrosion, especially in concrete structures or areas with high soil resistivity. However, they require periodic maintenance and monitoring, such as checking the cathodic protection test station and adjusting the DC current to ensure proper performance.
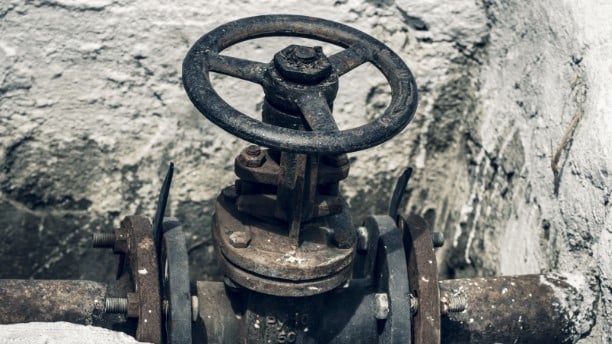
How Does a Cathodic Protection System Work?
The heart of this protection method lies in forming an electrochemical cell, which controls corrosion by redirecting the flow of electrical current. To understand the magic behind cathodic protection, you must first grasp the concept of a corrosion cell.
Picture this: when two dissimilar metals or areas with different electrochemical properties come into contact, a corrosion cell is formed. This process causes one of the metals to corrode more rapidly than the other, which can be particularly problematic for structures like gas pipelines and underground storage tanks.
Cathodic protection swoops in to save the day by disrupting this corrosive process. It works by making the entire structure act as the cathode (the less corroding part) within the corrosion cell, thus reducing the corrosion rate. This can be achieved through two primary methods: sacrificial and impressed current cathodic protection. Both methods protect numerous structures from corrosion and extend their service life.
Sacrificial Cathodic Protection
In a galvanic anode cathodic protection system called passive cathodic protection, sacrificial anodes play a significant role. Sacrificial anodes are made of an active metal, such as zinc, aluminum, or magnesium, which corrodes more quickly than protected structures. When the sacrificial anode is attached to the structure, it forms a galvanic cell, where the anode sacrifices itself by corroding instead of the protected area.
This electrochemical process occurs due to the potential difference between the sacrificial anode and the structure, causing anodic and cathodic electrochemical reactions. As the sacrificial anodes corrode, they produce a current density sufficient to protect the exposed steel from further corrosion.
Impressed Current CP Systems
On the other hand, the impressed current CP system is a type of active cathodic protection. This system utilizes an external power source to apply cathodic protection to the structure.
Instead of relying on a sacrificial anode, this system employs inert anodes, which don’t corrode easily. The current generated by the power source flows from the anode system to the buried metal structures, ultimately reducing the corrosion rate.
Cathodic protection system design is vital for the effectiveness of the CP system. Factors like the type of structure, soil resistance, and the environment in which it is placed affect the cathodic protection design.
Engineers carefully consider these factors to ensure that the chosen anode cathodic protection system works efficiently, whether it’s a galvanic anode system or an impressed current system.
Wrapping Up
Cathodic protection is a vital technique that can help you control corrosion in various applications. By implementing either galvanic cathodic protection or cathodic protection cp, you can effectively disrupt the corrosion cell process and extend the life of your assets.
Whether dealing with gas pipelines, underground storage tanks, or metal reinforcement bars, cathodic protection protects numerous structures and ensures their longevity. Don’t let corrosion control the fate of your valuable infrastructure.
If you’re considering a cathodic protection project, the experts at WildHeronDrilling are here to help. Call us at (916) 435-3555 or fill out our contact form, and we would be happy to answer any questions you may have.
We can also set up a consultation to discuss the project scope for your next Cathodic Protection endeavor. Don’t hesitate to reach out and safeguard your well pipelines and other structures from the damaging effects of corrosion.